Technical requirements The technical requirements for the centralized control system of the coal preparation plant are as follows:
(1) Achieve the main production process of the coal preparation plant start/stop automation centralized control system can be programmed to achieve the main process sequence start / stop, equipment / process selection or switching, logical relationship blocking, automatic / manual switching, local local manual priority And normal start/stop and emergency stop.
(2) Realize the dynamic graphic display and main process parameter display of the entire plant and sub-systems, as well as equipment fault diagnosis and automatic alarm functions, for the whole plant equipment operation status and major production processes.
(3) Position measurement is carried out for the end coal bunker, the in-wash bunker bunker, the product bunker bunker, the hand-selected bunker bunker and the washed stone bunker to achieve position management and automatic allocation. When the position exceeds the limit, it can be alarmed on the computer screen of the dispatch room and at the scene.
(4) Perform liquid level measurement on clean water tanks, circulating water tanks, centralized water tanks, and external drainage tanks, and achieve liquid level limit alarms.
(5) Set up electronic belts for automatic metering of incoming raw coal, washed coal and product coal to provide real-time data for class operations and various statistical and analytical reports.
(6) The deviation detection sensor is set on the main belt conveyor. When the belt runs to a certain degree, it will alarm on the computer screen and on the spot. The main motor is over-current protected and the shaft temperature alarm is set for the fan. When the motor is over-current due to various reasons, the fan shaft temperature exceeds the limit, and the alarm is issued on the computer screen of the dispatch room.
(7) The system computer network is interconnected with the all-mine automation network platform.
(8) According to the online and offline data of the centralized control system, prepare production reports and achieve scientific management.
(9) This system leaves certain hardware and software resources for future expansion.
The centralized control system of the coal preparation plant configures the centralized control system of the coal preparation plant, which is a distributed control network system composed of field devices, programmable control systems and monitoring workstations of the STEC series products of the Master Age, and it can be of the same type. Network interconnection can also be formed by interconnecting several similar types of networks with heterogeneous networks. The typical configuration of the centralized control system network of the coal preparation plant is shown in the figure below
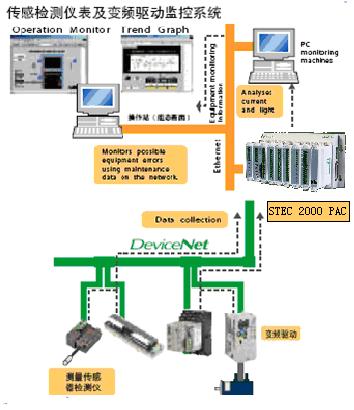
The monitoring workstation is set in the coal preparation plant dispatching room and consists of two operator stations and one engineer station. It monitors the workstation operation monitoring application software and controls the equipment through the master programmable controller system products and substations. Monitoring, data acquisition, transmission, processing, display of dynamic graphics.
The hardware configurations of the two operator stations are the same and they are backups. The monitoring software used the HOMS 5.0 monitoring system software or common configuration software (three-dimensional force control, MCGC, Kingview, etc.) of the Master Age. The operator station has an Ethernet interface and can provide a standard OPC server.
Monitoring workstation and PLC configuration Online UPS backup power system Plant-wide equipment sequence control and monitoring Coal preparation plant centralized control system Based on the coal preparation plant production equipment contact map and process flow chart, the main process equipment start/stop sequence control and operation Condition monitoring. According to the process selection to achieve device locking.
The measurement of raw coal and product coal measures the incoming wool, raw coal entering the plant and product coal, and sets up multiple electronic belt scales in the coal preparation plant. According to the electronic belt real-time data, the daily report and class operation report can be calculated, and the original coal gangue content, clean coal yield and coal slime production can be calculated.
Equipment fault diagnosis and alarms protect equipment, reduce the occurrence of failures, and reduce equipment damage. Fault detection and alarm devices are installed in major equipment.
(1) The belt conveyor deviation warning, set the deviation detection sensor on the belt conveyor, when the belt runs to the predetermined setting value, the alarm is given on the computer screen and on the site. The computer screen gives the offset position.
(2) Motor over-current alarms. Motor over-current detection sensors are installed in large-scale electrical equipment to detect phase loss and over-current caused by overload, blocking, bearing wear, and over-voltage. Give alarm information on the computer screen and on site.
(3) Axle temperature alarm, set the axis temperature alarm sensor in large fan or motor, when the shaft temperature exceeds a certain temperature, alarm on the scene and on the computer screen.
The alarm time and type can be stored in the monitoring computer database for query and statistics.
Position measurement and management The centralized control system of the coal preparation plant provides dynamic real-time detection of the main coal bunker and the meteorite bunker positions, making it easy for production dispatchers to direct production and ensure continuous production.
Automatic warehouse and warehouse management Through the real-time measurement of the coal bunker, the centralized control system of the coal preparation plant can automatically match the warehouse according to the real-time inspection of the warehouse, so that the warehouse is not empty or closed, so that production can be performed normally. Production command and dispatch personnel can grasp position status at any time to facilitate scheduling and command production. The historical data of positions can be queried and printed in the form of historical data or historical curves.
Level measurement Liquid level measurement is performed on clean water tanks, circulating water tanks, centralized water tanks, and drainage tanks. Ensure that the tank level, to meet production needs. Set high and low limit alarms to ensure that the water tank does not overflow and is not empty.
Level gauges should have local instructions and be able to implement data bit remote functions at the same time. The liquid level change data and dynamic graphics can be displayed in real time on the dispatch room computer monitor screen. Level history data can be queried and printed in the form of historical data or historical curves.
Ash content measurement and jigging production process control jigging coal washing process automatic control can effectively stabilize the fine coal ash, increase the clean coal yield, and has great economic efficiency. As we all know, the jigging process is a complex process in which multiple variables interact with each other. There is no effective solution so far. However, when the other conditions are fixed, it is an effective solution to achieve closed-loop control of the bed thickness in the first and second stages by adjusting the helium and medium coal. This method requires the buoy displacement sensor to measure the thickness of the first and second bed layers, and uses the same raw coal composition, feng shui system and other conditions as the calibration experimental conditions to set the bed thickness corresponding to the required clean coal ash. Closed-loop control of it. In the process of executing the closed-loop control program, the bed thickness is set to the set value by adjusting the quantity of coal rafts (and medium coal); when the raw coal quality, coal supply, feng shui and other changes, the jig driver can According to experience or by the calibration curve to change the size of the set value.
Concentrate Dosing Automatic Control System The coal preparation plant adopts a complete set of automatic dosing system to achieve automatic dosing of the slime water concentration system. The detection instrument of the dosing system enters the centralized control system of the coal preparation plant at the same time, realizing the real-time detection, statistics and management of the process parameters of the enrichment system.
Masterpiece product features:
1. The system adopts the highly modular and intelligent design of Master's SETC2000 series, which can handle the needs from simple to complex and can be used for large-scale remote monitoring;
2. The system's acquisition is through the analog channel (AI) and digital channel (DI) of the embedded collector at a maximum of 96 points. The means of expansion is to use a block of I/O modules through the expansion board in the form of a bus. connection. Provide plenty of smart sensor access ports, can be a large number of types of smart sensors. Control is achieved through the embedded controller's analog channel (AO) and digital channel (DO) at a maximum of 64 points.
3, the core of the embedded data acquisition device adopts the powerpc 32-bit CPU of the Motorola company in the United States with a frequency of 66 MHz. Embedded real-time Linux operating system is used to support users for secondary development and provide APIs for I/O devices.
4. The system is equipped with imported sensors, solenoid valves and other related equipment, which has the characteristics of sensitive response, high collection accuracy, accurate control, easy installation, easy maintenance and so on.
5, data storage using electronic hard disk (DOC), but also different requirements can store expansion.
6, support a variety of (Internet, telephone, GPRS, GPS, etc.) long-distance communication methods and protocols. Fault tolerance, automatic error correction for external interference or sudden sensor failure.