SAE predicts that by 2010, electronic equipment in cars will account for an average of 40% of the total price! In US dollars, the sales of independent semiconductor devices in 2008 were about 20 billion (from Databeans ’market survey). This number will decline in 2009 for well-known reasons, but this is temporary, because the car can no longer be without electronic equipment. The injection system, fuel control, navigation, and safety systems are all controlled by electronic equipment.
So, as test engineers, how should we deal with the complex testing of the next generation of Electronic Control Unit (ECU) before assembly? What kind of test system-what I want to emphasize is "system", there is no single ATE The platform can complete all the testing work-it is the most suitable. In this short article, I will try to make you more aware of various application and testing strategies. At least I hope to help you sort out your ideas, so that you can ask the system integrator and / or ATE supplier more accurately and help you make the right choice.
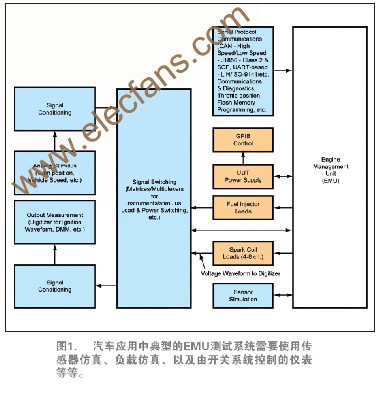
product development
Of course, all newly designed products must be verified and tested before release. HILs (Hardware In the Loop) become more and more important in laboratory testing strategies. In general, this is mainly used to test the response of the ECU when it encounters external fault conditions. General faults include: loss of signal, short circuit to ground or Vbat, or wrong data. In the ATE industry, a fault injection switching system (Fault InserTIons switching system) is usually selected to achieve this test. Several companies provide the hardware devices for fault generation / injection that I mentioned above. Because the safety of ECUs is critical in automobiles, high-level tests of this type are also very important.
Process testing
In the process of assembly and quality testing, the automotive industry appears somewhat conservative in introducing new technologies. According to the report of INEMI (InternaTIonal Electronics Manufacturing IniTIaTIve-http: //), the automotive industry lags behind other industries in the introduction of PCBs in small packages. The main influencing factor is the use environment-the temperature range is -40 ~ +250 degrees Celsius (the working temperature of the exhaust gas sensor can reach 580 degrees Celsius), and the vibration of multiple G requires its structural design standards to be much higher than that of general industries such as home computers. The original device density is also much lower than other consumer products. In addition, in the future, most of the clocks on the car will not exceed 150MHz, and the test point is still mechanically and electrically accessible. This information indicates that ICT testing (In-circuit testing online testing) will still occupy an important position on the assembly line in the next few years.
AOI (Automated Optical Inspection) is also very important. For ECUs with limited electrical connections, AOI is the most economical processing test method. Because automotive ECUs usually contain a lot of high power-and also large size-devices such as relays, coils, etc., the height of the camera during optical inspection and the ability to focus on the large and small devices on the ECU are very important.
For quality and reliability considerations, AXI (Automatic X-Ray Inspection) is also highly regarded as part of the test strategy in the automotive industry. Because the BGA package has a large number of device pins, it is very important to verify that all pins are firmly soldered, especially for those ECUs that involve safety: such as ABS anti-lock brake systems, airbag controllers, active safety systems and cables Transmission control (X by Wire), etc. Because the car's steering and braking (coming soon) are fully electronically controlled, these tests will be crucial in the near future.
Because the optical inspection can not see the part under the BGA chip, and in fact not all I / Os have terminals, the importance of AXI in the test strategy is increasing. Despite the impact of the economic recession in 2008 and 2009, the number of new cars purchased annually in the world is still as high as 50 million (data from Automotive News – http: //).
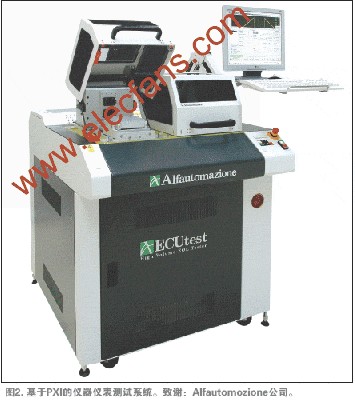
The detection speed of the current AXI system is very low (3D X-ray inspection is about 0.6 square inches / second, 2D X-ray inspection is about 6 square inches / second). If the inspection speed is increased, ATE manufacturers must also increase the analysis speed of the equipment accordingly, and the resulting cost increase is also an important consideration in the cost-sensitive automotive industry. In many cases, it is possible to ensure the efficiency of the production line by performing some X-ray inspections on the ECU and using AOI or ICT inspections on other parts.
Various types of needs
The complexity of EOL determines the difficulty of the test, because the task here is to simulate the real working environment, so to complete these complex tests requires a sound plan. ECU has some requirements to be considered in the functional test system, including:
Power requirements: The electronic control unit determines when to drive electromechanical devices such as motors and coils. According to the current 12V standard of the automotive power bus, this means that a lot of current may occur-electric power steering requires up to 100A! The variable valve actuator on the V8 engine requires a peak power of up to 2400W! Equivalent to a peak current at 12V Up to 200A! So proper switch specifications and cooling capacity are very important.
Hybrid vehicles: The cigarette lighter of the power system may be as high as 300V, but most peripheral equipment-such as lights, entertainment and on-board equipment-runs at a very low voltage. So there is usually voltage conversion in this type of design. And because the voltage of 300VDC is more dangerous, isolation testing must be considered in the test plan to ensure safety.
Serial communication: The automotive industry has accepted the concept of a network, or "multi-channel connection" according to their own statement-according to the connection structure of each ECU in the car. Multi-channel technology has been used to display information such as diagnosis, safety, and performance (for example, the speedometer is no longer driven by a separate cable), and is now also used in entertainment and navigation. However, the fact that too many protocols are used is a problem.
CAN (Controller Area Network) is the most widely used, and K-Line and LIN (Local Interconnect Network) are also widely used. There are other real-time protocols such as FlexRay and TTP (Time-Triggered Protocol) for telex wire control and active security protection, and optical fiber protocols such as MOST (Media Oriented System Transport) and IDB1394 (derived from IEEE-1394, or called FireWire), these protocols commonly used for entertainment and in-vehicle communication are currently mainly used for high-end cars, and can be applied to low-end products in the future if the price is reduced.
Some organizations such as AUTOSAR (Automotive Open System Architecture-http: //) are looking for ways to simplify ECU development and interconnected communication-but it will take some time to implement. So now whether you are buying or building a test system, you have to deal with a variety of different protocols.
RF applications: AM / FM broadcasting, RF and microwave testing have been more widely used in automotive ECU testing. The Bluetooth® interface connected to mobile phones has been widely used in low-cost automobiles. IEEE reported on the concept design of using BAP (Bluetooth Access Points) to establish a micro network. The goal of this design is to avoid conflicts in device identification. Finally, there is interactive cruise control, which mainly uses the radar band (40GHz) to maintain a safe distance.
Conclusion
Voltages from 12V to 300V-currents up to 200A-bandwidth from DC to lightwave-what a huge challenge! Obviously I am not here to give you all the answers-related books have fully explained these topics. But I hope that through this article you already have more ideas that can make your work easier-and make our cars safer and more comfortable.
Solar Pump can be applied to daily use (Groundwater) .Agricultural irrigation,foersty ieeigation,desert control,pasture animal husbandry,water supplier for islands,waste water treatment engineering and so on ,solar techsolar pumping system is depends on energy storing devices,and stors water instead of electricity.It improve the device,and at the same time it lowers the construction and maintenance cost if the system dramatically in recentyears , with the promotion of the utilization of new energy resouces,solar pumping system are widely used in municial engineering , city centre squares, parks ,turist sites,resorts and hotels ,the landscapes and fountain system in the residen tial areas.Advantages of solar photovoltaic water pump system
Fully automatic operation without manual duty.Suitable pump types are wide, such as three - phase, single - phase, direct - current pump.The input voltage range is wide, and a variety of photovoltaic modules are available.Modular design for easy maintenance.Use imported components, safe and reliable.Remote control.
Solar Pump
Solar Pump,Solar Water Pump,Solar Energy Pump,Recycle Solar Pump
ZHEJIANG FIZZ NEW ENERGY CO.,LTD , https://www.ywfizz.com